COLLATERAL EVENT
Particleworks European Users' Meeting
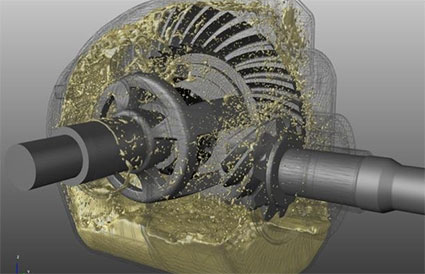
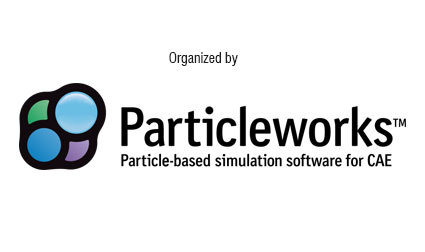
The first European User’s Meeting for Particleworks taking place on the second day of the International CAE Conference and Exhibition. Reduction of costs and development time, improvement of performances are some of the benefits of using particle-based CFD. The speakers will cover different industrial applications from the thermal management of e-drives and engines to the lubrication of bearings and gears of transmission systems for automotive, industrial and motorsport applications.
Particleworks Europe Introduction
This full presentation is not available
Abstract
Particleworks Europe is a JV between Prometech Software Inc. and EnginSoft S.p.A. and aims to establish, promote and manage the European distribution network of Prometech Software technologies and applications based on the Moving Particle Simulation (MPS) method.
Particleworks Europe will constitute the European competence center, both to support distributors and to assist customers who require help for complex applications, verticalization, dedicated developments or integration into their scientific information systems. Particleworks Europe will also aggregate needs and requirements of customers to ensure their rational inclusion in the Particleworks software development roadmap.
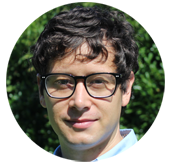
Riccardo Bergamin, ZECO
Michele Merelli, EnginSoft
Comparison between CFD and MPS Methods for Numerical Simulation of Pelton turbine
Abstract
CFD modelling and validation of Pelton turbines are challenging due to the transient and multi-phase nature of the flow, that require fine and high quality grid definition, in order to accurately capture the flow features.
Due to high computational time, modern CFD techniques allow to study and optimize the components of the turbine like single bucket, needle and nozzle, deviator and manifold.
Finite Volume CFD codes can be used for this kind of component simulations, but models become too complex and computationally expensive when the whole turbine and the open air casing are included in order to study jets interactions and water outflow.
Using particle-based Navier-Stokes solvers, like Particleworks and the Moving Particle Simulation method, these barriers can be overcome, with a technological breakthrough that paves the way to new study and optimization opportunities.
In this paper both Finite Volume simulations of turbine components and Moving Particle Simulation of a complete runner will be presented and comparisons with expected turbine efficiency will be shown.
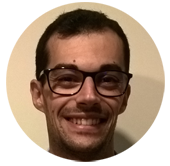
Francesco Canestri, Dana Motion Systems
G. Parma, EnginSoft SpA
A. Lucchi, Dana Motion Systems
M. Galbiati, EnginSoft SpA
Churning Losses Evaluation in Swashplate Axial Piston Pump using Moving Particle Approach
Abstract
In axial piston units, churning losses have a non-negligible influence on mechanical efficiency. This work presents a numerical approach for the evaluation of the churning losses in a swashplate axial piston pump for closed circuit applications using the MPS (Moving Particle Semi-implicit) software Particleworks.
Taking advantages of experimental activities and theoretical results derived by different authors [1,2,3], a sensitivity analysis is carried out in order to evaluate the influence of the numerical parameters involved in the simulation. In particular, the effects of the particle size, the slip factor applied to the wall boundaries and the turbulence model are analyzed.
In this framework, reduction of particle size clearly shows the convergence of the churning losses toward the expected value.
The paper also demonstrates that when the reduction of particle size is not affordable due to computational time and resources, the same torque results can be obtained with a coarser particle size, by increasing the slip factor, that affects the viscous forces on the walls.
The use of the turbulence model has instead a lower impact on the churning losses prediction with respect to particle size and slip factor.
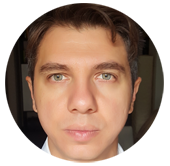
Carlo Arturo De Marco, CNH Industrial
Michele Coccetta, CNH Industrial
Lubrication and Churning Losses Estimation in Gearboxes for Agricultural Equipment
This full presentation is not available
Abstract
Agricultural Equipment and off-road applications are always equipped with complex gears transmission to transfer the torque from the power source to the final drive or the implements, the driveline of a tractor is the most representative example of such a system. In addition, different type of gearboxes, more or less complex and compact are also used to supply torque to different places and different mechanisms of the machines, this is the case of Combines and Forage Harvesters. The simulation of the gears lubrication based on conventional CFD approach is possible by using the most recent meshing techniques developed by the main CFD software houses, however it does not seem yet so appealing from an industrial development perspective that requires tools and methodologies accurate and fast further than able to deal with many gears in the same time. In order to comply with this needs other meshless technologies (MPS in this case) have been explored and then implemented in the recent years starting from very basic test cases up to more and more complicated gear systems.
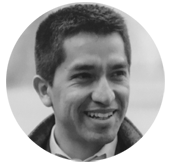
Oscar Cuevas, GIMA Transmission Technology
Gear oil jet lubrication efficiency
Abstract
In off-road and in-road vehicles, new developments look forward to improve the efficiency in order to reduce the CO2 emissions. About half of the total losses come from constant losses in the whole driveline. By reducing the gear churning losses, important savings can be made by reducing oil level but for that we need to lubricate gears by oil jet. The difficulty is to determine what are the oil flow and oil jet location to lubricate and cool gear correctly according gear speed/power and design (macrogeometry). The target is to design the lubrication pipes with the lowest cost impact with good lubrication oil flow efficiency. We have analyzed one gear train in different conditions with Particlesworks to establish a rule which gives lubrication oil flow efficiency. That allows to compare oil pipes design and inlet oil flow to take decision for cost effective solution.
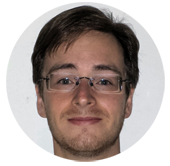
Nicola Pretto, MarelliMotori
Oil lubricated bearing support analysis on electric generators with mesh-less CFD methods
Abstract
In multibody complex dynamic systems it is often difficult to predict oil flow path and sometimes even impossible to simulate it with traditional CFD software.
This is a very important issue in the energy industry business, that is why Marelli Motori, a designer and manufacturer of electrical motors and generators since 1891, has tested Particleworks, an innovative mesh-less software based on the moving Particle Simulation (MPS Method).
This paper analyses the oil lubricated bearing support on electric generators: using this software our engineers are able to simulate the oil flow path inside the machine and model large-scale equipment behaviour before a new product is put into production, increasing its efficiency and avoiding possible critical issues at a later stage.
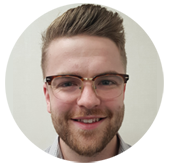
David Percival, EnginSoft
Rod Giles, Royal Enfield
Optimization of the Piston cooling oil jet using Particleworks with modeFRONTIER
Abstract
CFD simulations traditionally have an incredibly long computational time especially for cases involving free surface flows and moving parts with complex motion. Therefore, simulating the Piston cooling jet using traditional CFD would be impossible in a short time frame and simulation led design and design optimisation is totally unfeasible. However, by employing the MPS method with accelerated hardware, we are able to reduce the computational time to only 15 minutes and thus bring design optimization into the realms of feasibility.
This case demonstrates how we are able to modify the design of the cooling jet to optimize the cooling effect of the oil on the Piston thus improving reliability and life time of the Engine. We will also explore the techniques that were used to connect modeFRONTIER to Particleworks.
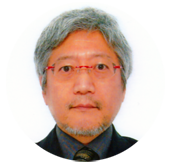
Sunao Tokura, Prometech Software
Recent Progress in Application Technique of Moving Particle Method
This full presentation is not available
Abstract
In recent years, applications of numerical simulation based on particle methods on the engineering problems, which are difficult to treat by means of conventional mesh-based CFD software, have been attempted and significant achievements can be obtained. The advantages of the particle methods are that it is easy to handle flow with complex free surfaces and moving boundary conditions which are typically seen in the problems including gears, pistons, and stirring blades. As such particle methods, SPH, MPS and other various methods have been proposed. However, regarding the application of particle methods and similar methods to the design and development of real industrial products, computational efficiency using large-scale model without degradation of accuracy is strongly required. Therefore, it is considered that MPS is suitable for application in such product development processes, since it shows remarkable computational efficiency. In addition, there is always requirement for the capabilities of the solver with high reliability, accuracy and efficiency in computation, as well as easy-to-use user interface settings to prepare and execute analysis tasks more simply and efficiently. In this presentation, the latest capabilities implemented in the CFD software Particleworks based on MPS method, are introduced and discussed.